Walmart Distribution Centers for Shippers
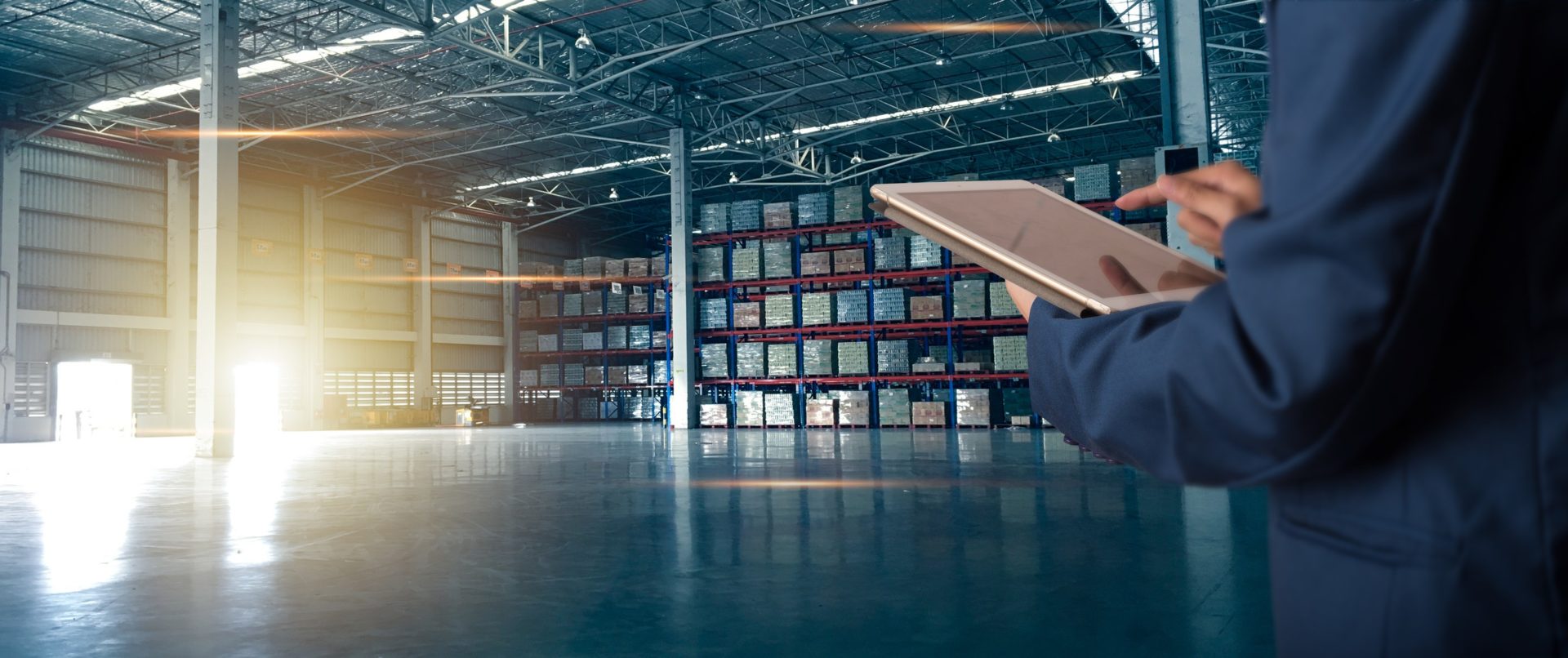
Everything you need to know about how Walmart distribution centers operate
Walmart opened for business in 1962 and became the world’s largest publicly-owned retail company in 1990 (a status that holds true today). As a shipper or supplier in logistics, one of the things you can do to move the needle in your business is partner with a large retailer like Walmart.While the future of retail can seem uncertain with new players like Amazon, getting your product into Walmart’s massive umbrella of stores or onto Walmart.com will increase sales and visibility for your brand. In 2020 alone, Walmart did $524 billion in gross sales. To service those orders, Walmart employed over 2.2 million associates worldwide.If you’ve already completed the multi-step process to get your product accepted by Walmart, congratulations! Now you will deliver your product to Walmart distribution centers, also known as a Walmart fulfillment center. Walmart’s distribution system is notoriously efficient, but it can be complex. Let’s break the process down.
Fast facts* on Walmart distribution centers
*pulled directly from Walmart’s website.
- Walmart has 158 distribution centers across the country, from Bentonville, Arkansas to Johnstown, New York — and everywhere in between.
- The distribution center network ships everything from general merchandise to perishable groceries to its Walmart and Sam’s Club stores.
- Each distribution center is more than 1 million square feet in size.
- Each distribution center employs more than 600 personnel who unload and ship over 200 trailers daily.
- Every distribution center supports 90 to 100 Walmart stores in a 150-mile radius, with new facilities and stores appearing each year.
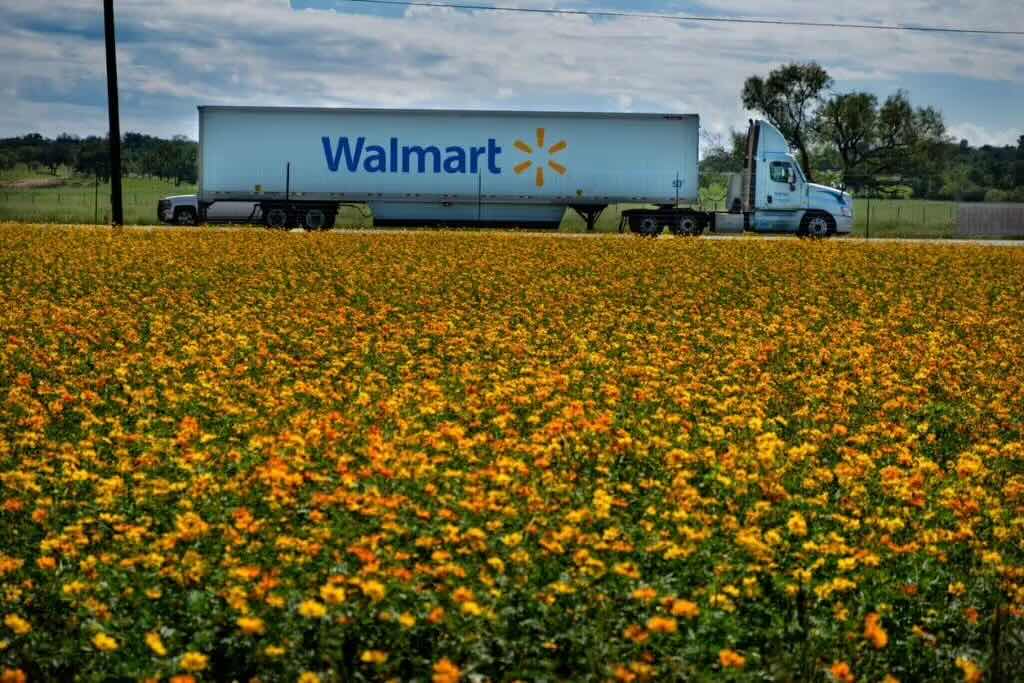
What makes Walmart’s distribution network different?
The supply chain in the United States and around the world is a complicated system. There are thousands of moving parts to get products from point A to point B. The Walmart distribution network is no different. Since its inception, however, Walmart has been dedicated to putting the efficiency of its supply chain at the forefront of its business model in order to keep costs low for consumers. This means Walmart uses innovative technology to manage its supply chain and consistently tightens requirements to maintain its cutting-edge approach. Walmart also works directly with manufacturers, which allows for a more streamlined approach, less risk in product movement, and an overall lower-cost supply chain. Walmart’s shipping model is entirely in-house, and its proprietary technologies allow for inventory assessments, product tracking, and more.
How does the Walmart distribution system work for shippers?
Let’s say you ship T-shirts. Here is how a T-shirt would go from manufacturing to a customer’s hands via the Walmart distribution system:
- Warehouse associates at the manufacturing plant load the pallet of T-shirts onto a truck.
- A truck driver transports cases of merchandise to one of Walmart’s regional distribution centers.
- A crew of freight handlers unloads the truck with a forklift and moves the product onto another truck.
- A truck driver hauls those T-shirts to their respective retail store within the Walmart network.
During this whole process, Walmart manages the inventory, restock needs, and customer data digitally.
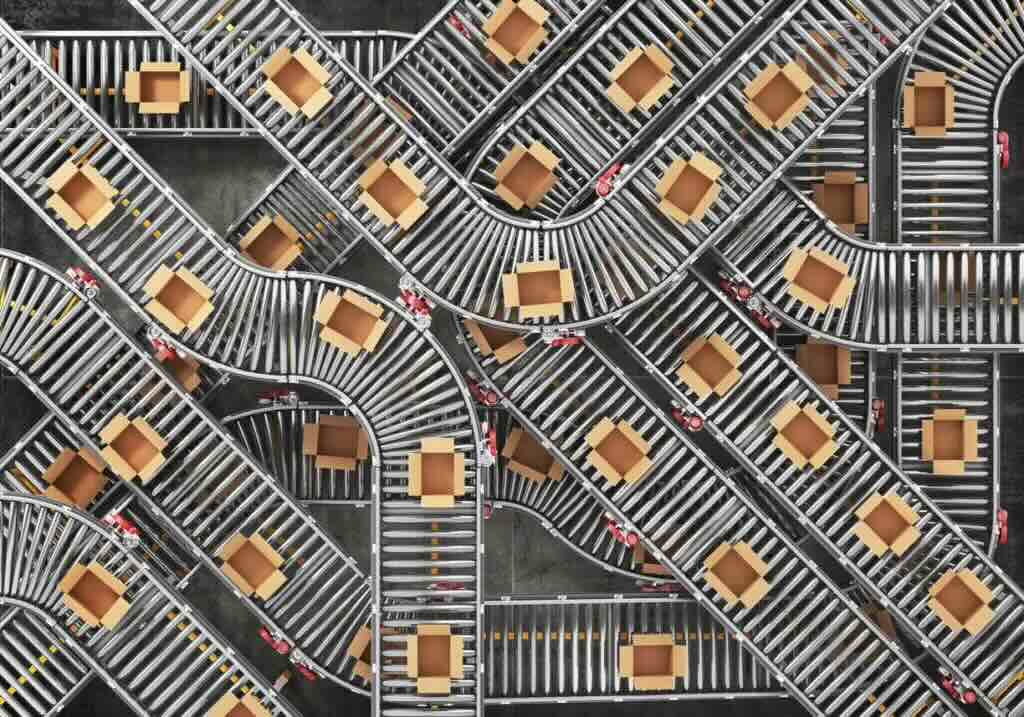
Tips for delivering to a Walmart distribution center
Delivering to Walmart for the first time? Here are some need-to-knows:
- Know the compliance rules. Because of the massive inbound volume of products (distribution centers see hundreds of trucks per hour), Walmart’s compliance rules are some of the strictest of any retailer. In 2020, Walmart warehouses tightened their already-stringent requirements. These requirements are part of the OTIF (On-time, in-full) initiative for Walmart. Learn more here.
- Be on time. Being on time as a Walmart shipper is a non-negotiable. If you are late more than once, there is a chance you may lose your product’s real estate or damage your relationship with the retailer. Ensure on-time delivery every time you drop off a shipment at a distribution center.
- Learn the Walmart technology. Walmart’s proprietary technology is called RetailLink. This technology handles all scheduling for drop-off appointments at Walmart distribution centers. As a supplier, once you are approved to work with Walmart, you will receive a RetailLink account and login information, plus resources to learn the product and track your product’s performance.
Walmart’s shipping requirements can feel complex and overwhelming, especially if you are a new shipper to the network. For a more thorough breakdown, read about Walmart’s shipping requirements here.
Adapting to The Walmart Way
In order to maintain a strong, long-term relationship with Walmart, you will need to follow all requirements and be on time, every time. But how do you ensure a seamless delivery in a risk-heavy industry? Flock Freight® can help. Using algorithmic technology, Flock Freight combines multiple shipments that are moving along the same route into one shared truckload. Shared truckload freight moves directly from its pickup location to its destination — without passing through hubs or terminals. Because your shipment never leaves the truck during transit, your freight incurs significantly less risk of damage and delay.If you’re a shipper for Walmart and want to deliver on time every time to Walmart distribution centers, join the Flock!