Outbound Logistics: Definition and Guide
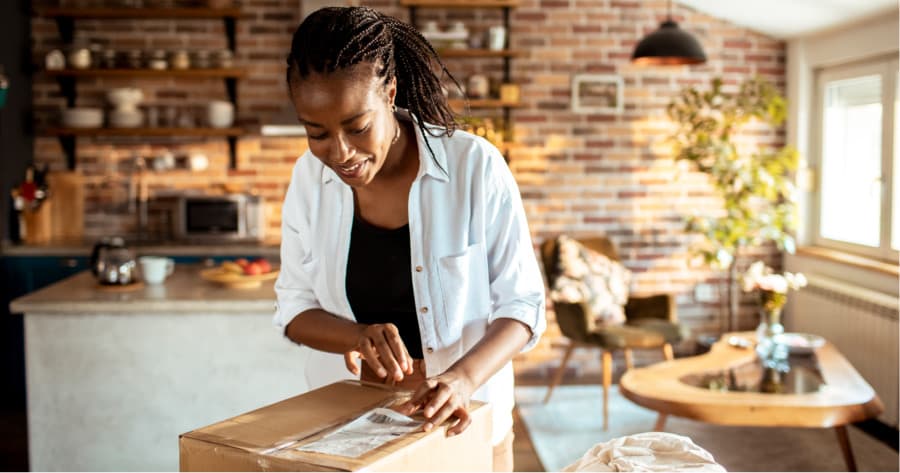
What are Outbound Logistics?
Outbound logistics play a crucial role in the smooth operation of businesses by managing the movement of goods from the production or storage facilities to the final consumers. It encompasses activities such as transportation, warehousing, and delivery, ensuring that products reach their intended destinations efficiently and effectively — the flip side of inbound logistics. In this article, we’ll delve into the various aspects of outbound logistics, including transportation, storage, delivery, integration with other supply chain functions, best practices, and how businesses can revolutionize their outbound logistics with the help of innovative solutions like Flock Freight.
Transportation in outbound logistics
Transportation is a vital component of outbound logistics, as it determines how goods are moved from one location to another. Businesses have a range of transportation modes to choose from, including air, sea, road, and rail.The selection of a transportation mode depends on factors such as speed, cost, and distance. Different modes of transportation services, such as full truckload (FTL), less-than-truckload (LTL), partial truckloads (PTL), and shared truckloads (STL), further cater to businesses' specific requirements.
Outbound shipping storage
Effective storage of outbound shipments is essential to ensure timely delivery and proper management of inventory. Businesses have various warehousing options available, including private, public, and third-party warehouses. Warehousing offers several benefits, such as efficient inventory management, risk mitigation, and cost savings through economies of scale. However, it also comes with challenges, such as space limitations, labor costs, and the need for robust security measures to protect stored goods.To address the challenges associated with outbound shipping storage, businesses can adopt several positive approaches that not only overcome these obstacles but also enhance their overall operations.
- Optimize space utilization: Efficient space management is crucial in maximizing the storage capacity of warehouses. Businesses can implement strategies like vertical stacking, utilizing mezzanine floors, and employing advanced storage systems such as automated racking systems or high-density storage solutions. These measures help maximize the utilization of available space, allowing for more shipments to be stored without the need for expanding the physical footprint.
- Implement lean inventory management: By adopting lean inventory management principles, businesses can reduce storage requirements and minimize the risk of overstocking or stockouts. Streamlining supply chain processes, optimizing order fulfillment, and utilizing just-in-time inventory practices can help minimize the need for excessive storage space and lower inventory carrying costs.
- Leverage technology: Embracing technological solutions can significantly improve outbound shipping storage operations. Implementing warehouse management systems (WMS) enables businesses to automate inventory tracking, improve order accuracy, and enhance overall warehouse efficiency. Additionally, using barcode scanning, RFID tags, or other automated identification methods can facilitate accurate and quick inventory management.
- Enhance security measures: Robust security measures are essential to protect stored goods from theft, damage, or unauthorized access. Installing surveillance systems, access control systems, and implementing stringent security protocols can help mitigate the risks associated with warehousing. Employing trained security personnel and conducting regular audits can further ensure the safety of stored shipments.
- Develop efficient workforce strategies: Labor costs are a significant challenge in warehousing operations. To address this, businesses can focus on developing efficient workforce strategies. This includes providing proper training to warehouse staff, implementing incentive programs to motivate employees, and optimizing work processes to minimize labor-intensive tasks. By creating a positive work environment, businesses can enhance productivity, reduce turnover rates, and control labor costs.
- Continuous improvement and performance monitoring: Regularly reviewing and analyzing outbound shipping storage operations can help identify areas for improvement. By monitoring key performance indicators (KPIs) such as storage capacity utilization, order processing time, and inventory accuracy, businesses can identify bottlenecks and implement targeted improvements. Continuous improvement initiatives ensure that operations stay efficient and adapt to changing business requirements.
By adopting these positive approaches, businesses can address the challenges associated with outbound shipping storage and contribute to streamlined operations, improved customer satisfaction, and increased profitability.
Delivery in outbound logistics
Delivery is the final stage of outbound logistics, where goods are transported from the warehouse or distribution center to the end customers. Businesses can choose from different delivery options, such as in-house delivery, courier services, or third-party logistics providers. The selection of a delivery option depends on factors like speed, cost, and customer expectations. Challenges in delivery include issues like traffic congestion, adverse weather conditions, and ensuring customer satisfaction through prompt and reliable service.To address the challenges in delivery during the final stage of outbound logistics, businesses can implement several positive strategies that focus on improving efficiency, customer satisfaction, and overall effectiveness, including:
- Route optimization: To combat traffic congestion and ensure timely deliveries, businesses can utilize technology and software solutions for route optimization. These tools help determine the most efficient routes, considering factors like traffic patterns, road conditions, and delivery schedules. By optimizing routes, businesses can minimize delays, save fuel costs, and enhance overall delivery performance.
- Weather monitoring and contingency plans: Adverse weather conditions can disrupt delivery schedules and cause delays. To overcome this challenge, businesses can implement weather monitoring systems that provide real-time updates on weather forecasts. With this information, they can proactively adjust delivery routes, reschedule shipments, or communicate potential delays to customers. Having contingency plans in place allows businesses to navigate through challenging weather conditions while minimizing disruptions.
- Enhancing communication: Prompt and reliable communication is crucial for ensuring customer satisfaction. Businesses can invest in robust communication channels to keep customers informed about their delivery status. This can include sending automated notifications about shipment updates, providing estimated delivery times, and offering tracking options. Clear and transparent communication helps manage customer expectations and builds trust in the delivery process.
- Collaboration with logistics partners, such as Flock Freight: If a business relies on third-party logistics providers or courier services, fostering strong partnerships and collaboration is essential. Regular communication and feedback exchanges help align expectations and ensure a shared focus on customer satisfaction. Working closely with logistics partners allows businesses to address challenges collectively, identify areas for improvement, and jointly develop strategies for enhancing delivery performance.
- Continuous improvement and data analysis: Regularly evaluating delivery performance and analyzing data can provide valuable insights for process improvement. By tracking key performance indicators (KPIs) such as delivery time, on-time delivery rate, and customer feedback, businesses can identify areas of strength and areas that need improvement. Leveraging data analysis, businesses can optimize their delivery operations, streamline processes, and make data-driven decisions to enhance overall efficiency.
- Employee training and empowerment: Ensuring that delivery personnel are well-trained and equipped with the necessary skills and tools is crucial for successful deliveries. Providing comprehensive training programs, including navigation techniques, customer service skills, and effective problem-solving, empowers employees to handle challenges proactively. Empowered delivery personnel can effectively manage unforeseen circumstances, address customer concerns, and represent the business in a positive light.
By implementing these positive strategies, businesses can overcome the challenges in delivery during outbound logistics. These approaches enhance efficiency, customer satisfaction, and overall effectiveness — resulting in a successful and seamless delivery process from the warehouse to the end customers.
Integration of outbound shipments
Integration of outbound logistics with other supply chain functions, such as procurement, manufacturing, and marketing, is crucial for seamless operations. It ensures effective coordination and information sharing across different departments, leading to improved efficiency, cost savings, and enhanced customer satisfaction. However, achieving integration poses challenges like data management, communication, and coordination among diverse stakeholders involved in the supply chain.By implementing the following strategies, businesses can enhance their outbound logistics and integrate it smoothly with other supply chain functions, such as procurement, manufacturing, and marketing:
- Implement robust data management systems: Investing in advanced data management systems can help overcome the challenge of data management. By utilizing integrated software solutions, companies can ensure that data flows seamlessly across different departments, enabling real-time access to accurate information. This not only facilitates effective decision-making but also improves overall operational efficiency.
- Foster effective communication channels: Establishing clear and efficient communication channels among diverse stakeholders involved in the supply chain is essential. By leveraging technology and utilizing collaborative platforms, organizations can enhance communication and information sharing. Regular meetings, conference calls, and the use of digital communication tools enable stakeholders to stay updated and address any issues promptly.
- Encourage collaboration and coordination: Promoting a culture of collaboration and coordination is vital for successful integration. This can be achieved through cross-functional teams and joint initiatives that bring together representatives from different departments. By encouraging open dialogue and sharing knowledge, organizations can break down silos and foster a collaborative environment where stakeholders work together towards shared goals.
- Standardize processes and procedures: Standardizing processes and procedures across different supply chain functions can help streamline operations and improve integration. By establishing clear guidelines and protocols, organizations can ensure consistency and eliminate inefficiencies. This includes aligning terminology, data formats, and reporting structures to facilitate smooth information exchange.
- Invest in training and skill development: Providing comprehensive training programs to employees involved in the supply chain can address the challenge of diverse stakeholder coordination. By enhancing their understanding of the overall supply chain and their specific roles within it, organizations can empower individuals to work together more effectively. This training can cover topics such as supply chain management, effective communication, and cross-functional collaboration.
The seamless coordination and information sharing across departments will enable businesses to respond quickly to market demands, optimize resources, and deliver products and services in a timely manner.
Best practices for outbound logistics
To optimize outbound logistics, businesses can adopt various best practices — including strategies like route planning, load consolidation, and order tracking to maximize efficiency and minimize costs. Performance metrics such as on-time delivery, order accuracy, and cost per delivery help businesses measure their outbound logistics performance and identify areas for improvement. Continuous improvement is crucial, and it involves activities like collecting feedback from customers and stakeholders, analyzing data to identify bottlenecks, and optimizing processes to enhance overall performance.Here are a few more detailed examples of best practices that businesses can implement to optimize their outbound logistics:
- Warehouse layout optimization: Efficient warehouse layout plays a significant role in streamlining outbound logistics. By organizing the warehouse strategically, businesses can reduce the time and effort required to locate and retrieve products for shipping. This can be achieved by grouping similar products together, implementing a logical storage system, and using technology such as barcode scanning or RFID tagging to improve inventory accuracy.
- Transportation mode selection: Choosing the appropriate transportation mode based on the nature of the products and delivery requirements can significantly impact outbound logistics efficiency. For example, air freight may be the best option for time-sensitive or high-value goods, while sea freight may be more cost-effective for bulk shipments. By analyzing factors such as transit time, cost, reliability, and environmental impact, businesses can optimize their transportation mode selection.
- Collaboration and partnership: Collaboration with logistics service providers such as Flock Freight, carriers, and suppliers can help businesses optimize their outbound logistics. By establishing strong relationships and partnerships, companies can leverage the expertise and resources of these entities to improve efficiency. This can include initiatives like sharing transportation resources, implementing cross-docking strategies, or outsourcing certain aspects of the logistics process to specialized service providers.
- Inventory management: Effective inventory management is essential for optimizing outbound logistics. By implementing inventory control techniques such as just-in-time (JIT) or vendor-managed inventory (VMI), businesses can reduce excess stock, minimize holding costs, and ensure timely availability of products for outbound shipments. Utilizing inventory management software or systems can provide real-time visibility into inventory levels, enabling better planning and forecasting.
- Automation and technology integration: Leveraging automation and integrating technology solutions can significantly enhance outbound logistics efficiency. Automation can be applied to various aspects, such as order processing, picking and packing, and labeling. Adopting a warehouse management system (WMS) or a transportation management system (TMS) can streamline processes, improve visibility, and optimize resource utilization.
By implementing these optimization practices, businesses can achieve better control over their outbound logistics operations, reduce costs, improve customer satisfaction, and gain a competitive edge in the market.
Revolutionize your outbound logistics: Turn to Flock Freight for faster, more efficient shipping
In conclusion, outbound logistics play a pivotal role in ensuring the smooth flow of goods from businesses to customers. It involves transportation, storage, delivery, and integration with other supply chain functions. By implementing best practices and leveraging innovative solutions like Flock Freight, businesses can revolutionize their outbound logistics practices, leading to faster and more efficient shipping, improved customer satisfaction, and a competitive edge in the market. It's time for businesses to prioritize outbound logistics and unlock their full potential for success.Join the Flock now, and take your outbound logistics to the next level.