7 challenges of the food and beverage supply chain
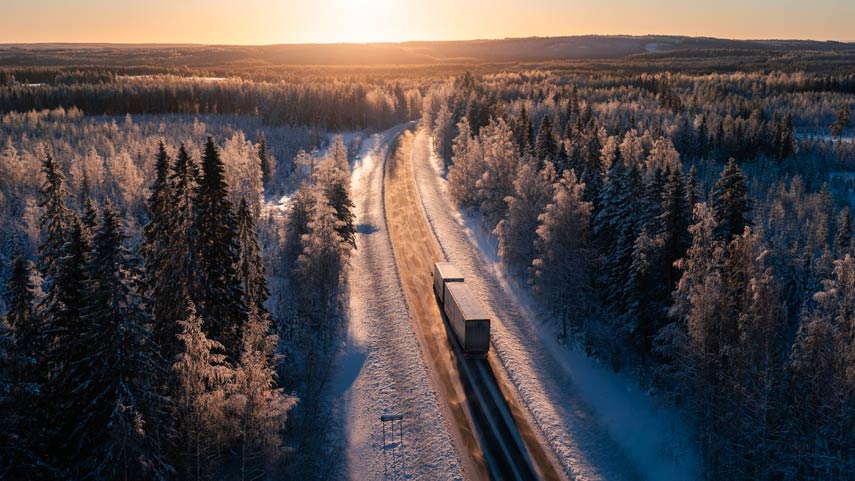
The food and beverage industry is competitive. Customers seek high quality at low prices and are often willing to switch brands. One misstep can cause spoilage and recalls.
The unique supply chain issues with food and beverage that shippers and carriers face has increased over the years—especially as the economy fluctuates and the freight industry experiences rising costs. Here are the top seven food and beverage supply chain challenges and how to combat them.
1. Safety and quality controls
Regulations help ensure that products are safe, but can also drive up costs and increase food and beverage supply chain challenges. The biggest regulation affecting food transportation is the rule on Sanitary Transportation of Human and Animal Food, part of the FDA’s Food Safety Modernization Act (FSMA). It applies to carriers, shippers, loaders, and receivers who transport goods by rail or road, but much of the responsibility falls on shippers, including:
- Determining appropriate operations
- Ensuring sanitation of vehicles and other equipment
- Ensuring adequate refrigeration when shipping perishables
- Preventing cross-contamination from previous loads
Shippers can transfer these responsibilities to carriers via contract. The carrier must then provide training for their team and follow all protocols. Carriers must also keep records of all contracts and training.
2. Keeping track of products
Recalls are a major food supply chain challenge, costing companies millions each year. Consumers are also becoming more aware of the origins of their food. With the rise of “farm-to-fork” dining, organic foods, sustainable foods, and more, many brands need to track their ingredients and materials throughout the sourcing, preparing, and shipping processes.
Beyond consumer preferences, traceability can help businesses identify gaps and risk factors in their supply chain. By updating technology, implementing digital processes, and leveraging freight tracking and visibility, food and beverage shippers and carriers alike can streamline their processes.
3. Cost restrictions
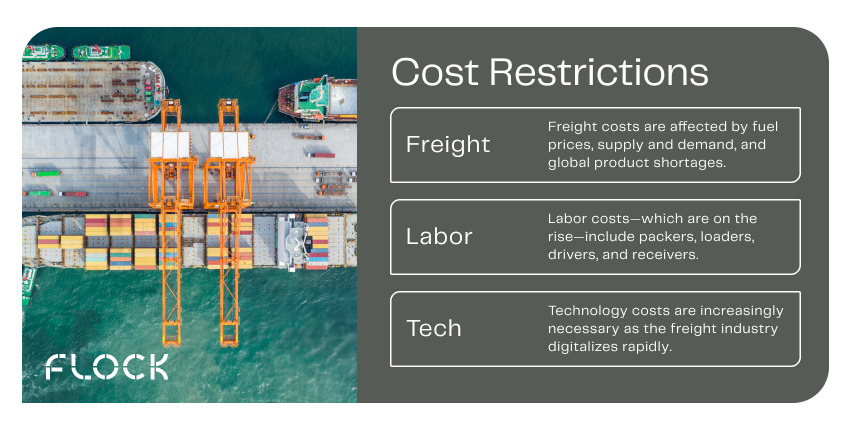
In this competitive industry, the pressure to keep costs low is high. These costs include:
- Freight costs – which are affected by fuel prices, supply and demand, and global product shortages.
- Labor costs – which are on the rise and include packers, loaders, drivers, and receivers.
- Technology costs – which are increasingly necessary in the rapidly digitalizing freight industry.
Changing costs can cause truck shortages, labor shortages, and inefficiencies that increase supply chain issues in food and beverage. Yet you also need to get goods to your customers on time and in full (OTIF), or you could be subject to OTIF fees at distribution centers.
A comprehensive cost-reduction strategy, including exploring new shipping modes, can help mitigate the effects of rising costs while keeping your shipments on time.
4. Communication gaps
Supply chain issues in the food industry involve a complex and global web of shippers, carriers, and suppliers. Each player often operates in a silo, unaware of the others’ actions. This lack of communication can cause inefficiencies and mistakes. Those errors can cause delays. And those delays, in turn, can cause food spoilage, contamination, and recalls.
Luckily, technology has made it easier than ever to see your entire food supply chain, while freight tracking and new shipping modes can help reduce delays. A spoiled load or a recall will cost your company much more than investing in these new technologies.
5. Damaged goods
As in many industries, smaller food and beverage shippers often cannot utilize full truckload (TL) and must rely on less than truckload (LTL) shipping. But LTL has a high incidence of one of the biggest food industry supply chain issues: damaged goods. In fact, 86% of shippers in 2022 had to replace and reship goods due to damage.
LTL can damage your shipment because:
- The hub-and-spoke model means freight is handled more frequently
- Freight moves through multiple facilities
- Freight from various shippers may not be as tightly packed
Shared truckload (STL) eliminates the damage-prone hub-and-spoke model. Shipments stay safe, terminal-free, and in a single truck, driven by a single driver, all the way to their destinations.
6. Problems with packaging
From the cost of stretch film to shipping container fluctuations, packaging can introduce some of the biggest supply chain issues in food and beverage. Material shortages mean companies need to find new sources or switch their packaging format. It can also result in packaging fraud, which is when producers substitute materials or use additional chemicals that can affect seal integrity and product preservation.
Global supply chain problems can even disrupt the availability of shipping containers. During and just after the pandemic, there was a shortage of containers. Today we may be facing the opposite problem: An oversupply of containers as the economy normalizes and consumer demand drops.
7. Unexpected events
Global pandemics aren’t the only unexpected event that can cause food and beverage supply chain challenges. Wars and conflicts cause shortages, like the current grain shortage. Border blockades prevent the flow of goods. Accidents, like the 2021 grounding of a container ship in the Suez Canal, can bring a shipping lane to a grinding halt.
Weather can create major issues as well. Ice and snow cause delays. Hurricanes damage warehouses and distribution centers. Heat waves—and resulting blackouts—can disrupt refrigeration and storage.
While you can’t prevent these events, you can be prepared for them: Shippers and carriers should evaluate their risk and have plans in place.
How shared truckload helps you tackle food and beverage supply chain challenges
The technology, processes, and freight modes you choose can help you reduce costs, unlock new operational efficiencies, and overcome food supply chain challenges like delays and damage. Flock Freight offers both patented technology and a novel freight mode—shared truckload—that benefits both shippers and carriers.
Our FlockDirect® platform finds and fills trucks’ empty spaces, so shippers only pay for the space they need and carriers fill their trucks and keep their drivers moving. That means happier drivers, happier suppliers, and happier customers. See how shared truckload is making an impact in the food industry and beyond on our industry hub page.